2020. 2. 28. 15:15ㆍ카테고리 없음
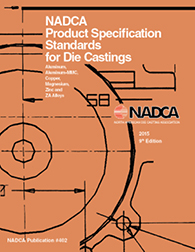
Die Casting Design Guidelines Pdf

Aluminium Die Casting Handbook
Casting Design HandbookINTRODUCTIONThe casting industry is one filled with mystery,science and art. Founding is the second oldest profession. Castings datingback to at least 4000 B.C. Were made in ancient China.
In spite of thatfact, it is a business that can be mysterious and intimidating to anoutsider. Hopefully this site will help thecasting designer, user and buyer get more out of the process.There are sections on foundry processes, castingdesign, tolerances of sand castings, quality assurance methods specific tofoundries, an alloy selection guide for nonferrous sand casting alloys and acollection of metalcasting glossaries.Be sure that you make your design efforts pay. Considerthe end use of the component and weigh the costs of the casting, machiningand design process to determine the amount of time you put in up front.A precision component that gets complex machining,is seen by the ultimate consumer, carries heavy load and is made by thethousands should receive a great deal of attention in the design phase tominimize costs at every step of the way later on.This site will spend a smallamount of time outlining the many processes available to the design engineerbut its concentration will be on nonferrous sand castings. The designer willfind that the section on design principles will be useful no matter whatprocess or what alloy is to be used.We are very grateful to The Aluminum Association forpermission to reproduce their engineering standards. The entire section ontolerances is excerpted from their standards handbook number 18.The recommendations contained in thissite are not intended as specifications. They arepresented as guidelines. Good judgment is an essential ingredient of anydesign endeavor.
Die Casting Handbook 2016
Nearly two-thirds of the aluminum castings made in North America are produced using high-pressure die casting techniques. This article compares and contrasts traditional high-pressure die casting with an improved version that uses a vacuum to pull air out of the die in order to reduce porosity in as-cast parts. It begins by describing a typical cycle for a traditional cold-chamber die casting machine, using detailed illustrations to show how gas can become trapped in the liquid metal. It then presents various remedies, ultimately focusing on vacuum die casting for the production of high-integrity parts. In addition to vacuum technology, the article discusses casting alloys, dies, and cells, and describes some of the benefits of structural die castings.